Top Techniques for Optimizing Steel Construction Processes for Maximum Effectiveness
From thorough design planning to accepting advanced technologies, the mission for maximum effectiveness in steel fabrication entails a multifaceted strategy. Allow's check out how these approaches can change steel construction procedures, paving the means for unprecedented effectiveness and competitiveness in the market.
Reliable Design Planning
In the world of steel fabrication processes, reliable and strategic layout preparation plays a pivotal function in simplifying production process and optimizing operational performance. The layout of a steel construction center straight impacts the effectiveness of operations, material circulation, and employee performance. By thoroughly creating the setup of equipment, workstations, storage space locations, and material handling equipment, business can dramatically reduce unnecessary activity, minimize material dealing with times, and enhance the general manufacturing procedure.
A reliable design strategy takes into consideration factors such as workflow sequences, proximity of workstations, material handling paths, and safety and security regulations. It intends to produce a sensible and structured flow of activities from raw material intake to the final product dispatch. Through effective layout planning, companies can eliminate bottlenecks, reduce manufacturing downtime, and improve the overall operational efficiency of the steel fabrication procedure.
Furthermore, a well-balanced format strategy allows much better usage of offered space, improved interaction in between employees, and improved safety practices within the center. On the whole, spending time and resources in establishing an effective layout strategy can produce substantial benefits in terms of enhanced productivity and price savings for steel fabrication businesses.
Advanced Reducing Technologies
Using advanced technologies in steel manufacture processes boosts accuracy, efficiency, and general production quality. Advanced reducing technologies play a crucial duty in improving procedures and maximizing the fabrication procedure. One of one of the most popular advancements in this area is the implementation of laser reducing systems. Laser cutting deals exceptional accuracy, enabling for intricate styles and intricate shapes to be cut with marginal product wastage. Furthermore, plasma reducing technology has actually also transformed steel fabrication by allowing swift and precise puncturing electrically conductive materials. This method is especially effective for cutting thick steel plates with speed and accuracy. Water jet cutting is one more ingenious innovation that makes use of a high-pressure stream of water to puncture different kinds of materials, consisting of steel, with phenomenal precision. By incorporating these sophisticated reducing technologies into steel manufacture processes, makers can significantly increase effectiveness, minimize manufacturing times, and inevitably boost the quality of their products.
Automated Welding Equipments
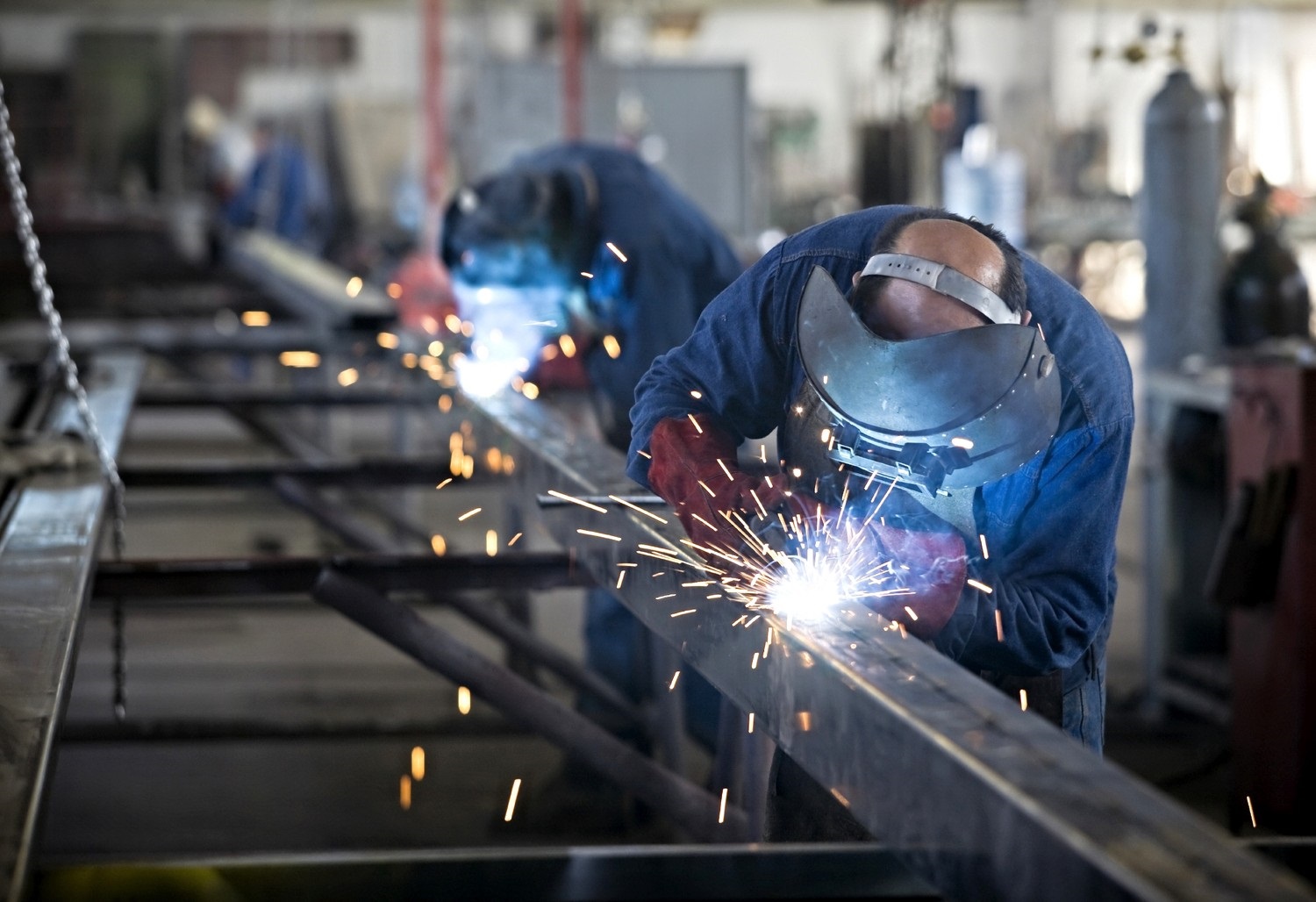
One of the vital advantages of automated welding systems is their capacity to maintain a high degree of accuracy throughout the welding procedure. The precision supplied by these systems guarantees that welds are consistent and satisfy the called for specifications, bring about more powerful and extra trustworthy metal structures. In addition, automated welding systems decrease the danger of human error, leading to less problems and remodel.
Furthermore, these systems can deal with intricate welding tasks with ease, consisting of welding in limited spaces or on rounded surface areas. This versatility makes automated welding systems appropriate for a wide variety of steel fabrication applications, from massive commercial projects to detailed customized styles. Overall, the implementation of automated welding systems in steel construction procedures significantly improves effectiveness, high quality, and overall task end results.
Stock Administration Solutions
Enhancing operational efficiency and enhancing procedures, efficient stock administration options play a critical role in optimizing steel fabrication operations. By carrying out robust inventory management systems, steel fabrication firms can ensure that the right materials are readily available when required, decreasing disturbances and hold-ups in production schedules. Making use of innovative software program options enables for real-time tracking of inventory degrees, allowing precise forecasting of product needs and stopping stockouts or overstock circumstances.
Furthermore, inventory monitoring remedies aid in minimizing carrying prices connected with excess supply and enhance capital by straightening stock degrees with real demand. By classifying materials based upon use frequency and urgency, view it producers can prioritize purchase and storage space appropriation, additionally enhancing operational efficiency. In addition, executing barcode or RFID technology assists in accurate supply tracking and streamlines the tracking of product motions within the center.
Constant Refine Improvement
To construct upon the gains made through reliable stock monitoring options, the emphasis now changes towards driving constant procedure enhancement within steel manufacture operations. Constant procedure enhancement is an organized approach targeted at boosting effectiveness, lowering waste, and enhancing general top quality throughout the fabrication procedure. By applying a culture of continuous improvement, steel fabrication firms can identify traffic jams, streamline process, and enhance resources to take full advantage of performance.
One secret element of continual process renovation in steel fabrication is the routine evaluation and evaluation of production procedures. This includes event comments from workers, monitoring vital efficiency indicators, and identifying areas for improvement. By leveraging data-driven insights, firms can make educated decisions to drive meaningful modifications that positively impact operations.
Moreover, adopting lean production principles can considerably add to process enhancement in steel construction. Alpha reo. Strategies such as worth stream mapping, 5S organization, and Kaizen events can assist remove non-value-added tasks, systematize processes, and cultivate a culture of innovation and continuous knowing within the organization
Final Thought
In verdict, optimizing steel fabrication procedures for optimal performance calls for careful planning, utilizing innovative cutting technologies, implementing automated welding systems, managing supply successfully, and constantly boosting procedures. By including these strategies, makers can improve performance, minimize prices, and boost overall performance in the steel construction market.
Through effective design preparation, companies can remove bottlenecks, lower production downtime, and enhance the general functional performance of the steel manufacture process. steel fixing.
Utilizing sophisticated innovations in steel manufacture processes boosts precision, performance, and general production top quality. By including these innovative reducing innovations into steel manufacture processes, manufacturers can considerably enhance performance, decrease production times, and inevitably boost the quality of their you can check here items.
On the whole, the execution of automated welding systems in steel construction procedures considerably enhances efficiency, high quality, and general project outcomes.
One secret element of constant process improvement in steel fabrication is the routine review and evaluation of production procedures. (metal fabrication melbourne)
Comments on “Advanced Steel Fabrication Melbourne: Building the Future Today”